Automobili elettriche urbane leggere e modulari
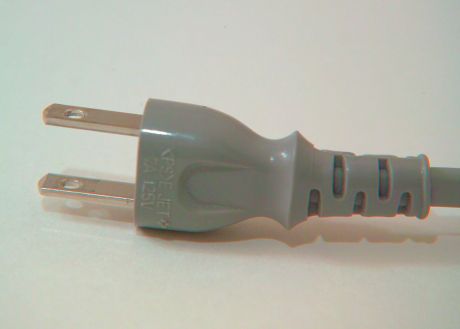
JapanesePlug
By No machine-readable author provided. Fg2 assumed (based on copyright claims). [Public domain], via Wikimedia Commons
I veicoli completamente elettrici si stanno avvicinando al diventare una realtà grazie allo sviluppo di innovative architetture per la scocca Body in White che usano alluminio leggero e materiali compositi evoluti.
EVOLUTION (The Electric Vehicle revOLUTION enabled by advanced materials
highly hybridized into lightweight components for easy integration and
dismantling providing a reduced life cycle cost logic) sta utilizzando
la concept car Pininfarina Nido come riferimento per le sue attività.
L’attuale concetto Body in White (BiW) riferito alla scocca è stato
completamente rivisto mediante una strategia di progettazione mirata a
ridurre il numero di parti e che usa tecnologie innovative legate ai
materiali leggeri.
Allo scopo di passare facilmente da bassi ad alti volumi di produzione, il modello di carrozzeria scelto con una cella centrale è uno standard consolidato se si considera lo schema del processo di assemblaggio. In pratica, la cella ha una funzione strutturale, mentre la parte anteriore è dimensionata per assorbire l’energia durante uno scontro frontale e la parte posteriore è concepita per essere modulare, consentendo la trasformazione in versioni monovolume e furgone.
Le tecnologie Al prese in considerazione e applicate su leghe Al 5xxx-6xxx e 7xxx forniscono le opportunità di ottenere delle parti con geometrie complicate e ridotto spessore, unendo parti differenti in un unico elemento. Inoltre, è possibile lavorare un elemento con una singola operazione e spessori variabili.
Una tecnica di “fusione in sabbia verde” consente di ottenere giunzioni stampate assieme tra differenti elementi prodotti con diversi processi di produzione.
La riduzione del costo e la semplificazione del processo possibili in termini di tempo e assemblaggio sono promettenti: l’attuale tecnologia all’avanguardia, basata su stampi tradizionali, non consente queste opportunità.
Il BiW è stato reso ibrido in una certa area del sottoscocca con un materiale composito della famiglia PA, rinforzato con GF. Questo materiale è stato ottenuto migliorando i materiali esistenti e sviluppando un processo di produzione idoneo per essere ridimensionato in base ai requisiti commerciali, attraverso un metodo avanzato di termoformatura del pannello e di iniezione 3D (processo CaproCAST).
Nuovi nanocompositi di polipropilene (pnc) basati su silicati stratificati e fibre di vetro hanno dimostrato robustezza e rigidità migliorate e sono stati scelti per dimostratori della barra trasversale e della portiera. Schiume di poliuretano basate su polimeri riciclati vengono studiate per essere usate come imbottitura sostenibile per assorbire l’energia in sezioni della barra trasversale.
Degli adesivi strutturali epossidici sono stati presi in considerazione per unire le parti del BiW e i punti di saldatura sono stati ridotti di numero: in certe aree i punti di saldatura sono stati usati solo per fissare provvisoriamente le parti durante la polimerizzazione.
Oltre ai precedenti risultati, il peso attuale del BiW è di 115 kg rispetto ai 160 kg dell’automobile di riferimento. Un’analisi mediante metodo degli elementi finiti sul veicolo virtuale intero mette in evidenza un buon comportamento strutturale, in considerazione degli standard UE per le prove d’impatto relativi a omologazione e prestazioni globali statiche e dinamiche.
L’architettura innovativa e l’integrazione di materiali leggeri farà sì che l’UE mantenga la sua competitività rispetto alle industrie automobilistiche asiatiche e statunitensi.
pubblicato: 2015-11-23